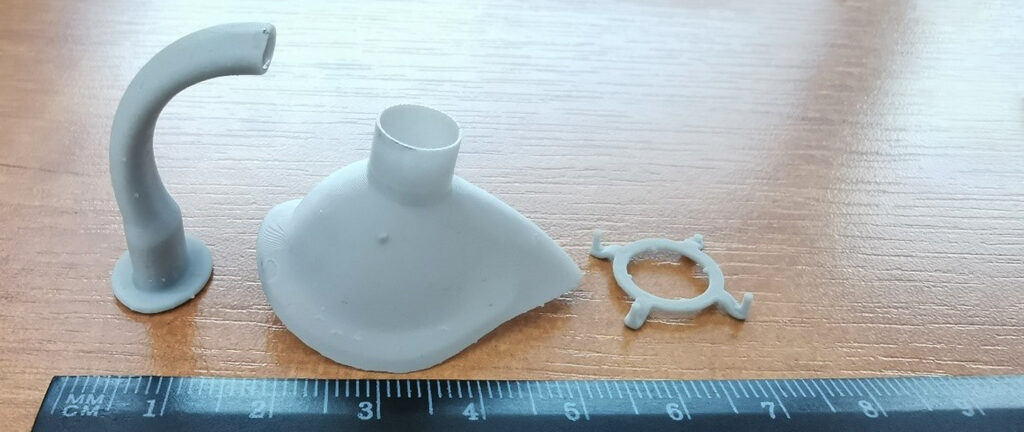
Edvinas Skliutas, Sima Rekštytė, Mangirdas Malinauskas* (VU) | Migle Lebedevaitė, Sigita Kašėtaitė, Jolita Ostrauskaitė (KTU) | Saulius Lileikis (3DC)
VU – Laser Research Center, Physics Faculty, Vilnius University, Saulėtekio Ave. 10, Vilnius, LT-10223, Lithuania | KTU – Department of Polymer Chemistry and Technology, Kaunas University of Technology, Radvilenu Rd. 19, LT-50254, Kaunas, Lithuania | 3DC – 3D Creative Ltd., Mokslininku St. 2a, Vilnius, LT-08412, Lithuania
Contact: mangirdas.malinauskas@ff.vu.lt
Based on the previous Vilnius University (VU), Kaunas University of Technology (KTU), and 3D Creative (3DC) collaborative achievement – a development of bio-based resin for multi-scale optical 3D printing (Fig. 1 [1]), the Team has succeeded to implement it for manufacturing of custom medical fittings. Such components are in unexpected yet urgent demand (especially in the shadow of a pandemic) and in hard to project amounts.
Rapid solution
The fittings are used in a clinical environment as different producers have different standards for various mounts, couplers, splitters, masks, etc. Thus, stocking up for all possible combinations would create huge and overestimated expenses, yet the need for them can be difficult to fulfill if manufacturing lines and transnational delivery is disrupted. So, the local and flexible production, enabled by optical 3D printing, seems a rapid solution for solving such a problem. And if the applied material is bio-derived (bio-renewable content can be > 80%) – it solves time, transportation, price and ecological issues simultaneously.
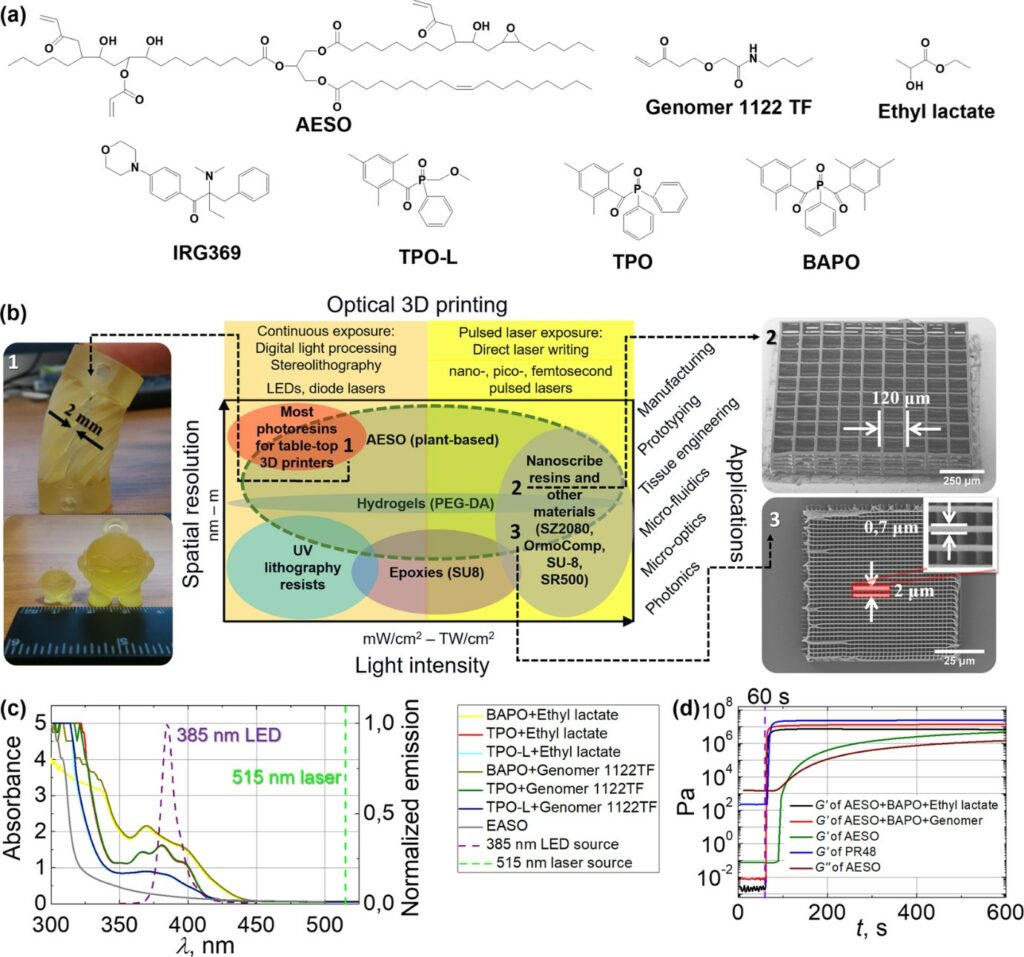
Optical 3D printing as an additive manufacturing tool was used for the production of custom medical devices: firstly, specific plant-based resins were synthesized at KTU, later, they were tested for small scale printing at VU, and, lastly – produced at the industrial line in 3D Creative. The Computer Aided Design (CAD) models were obtained using the 3D scanning technique readily available at 3D Creative. They were converted to STL models and adjusted for specific 3D printers: Asiga Pico 2 UV (VU) and Zortrax Inkspire (3D Creative) (see Fig. 2 and 3).
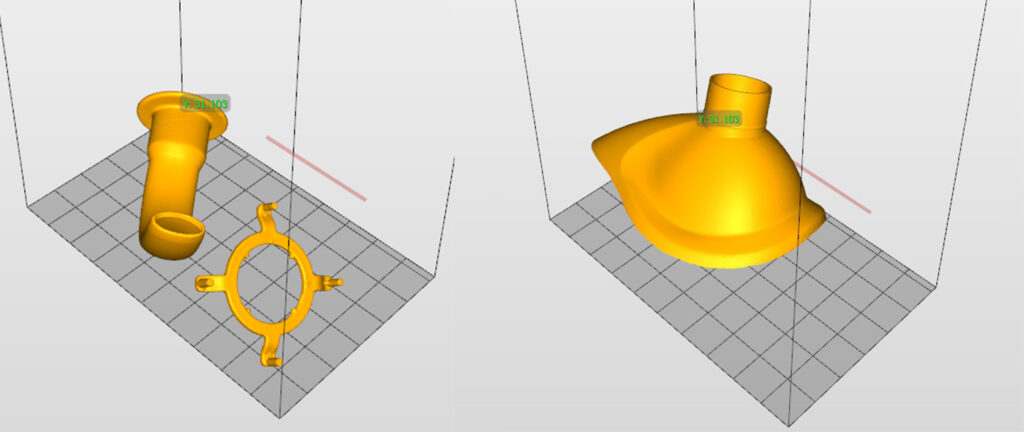
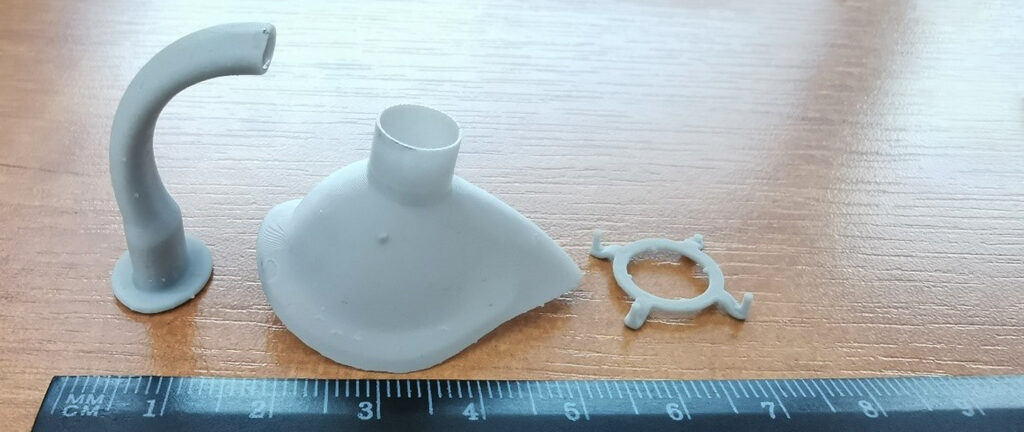
A systematic variation of 3D printing parameters like layer height and exposure duration was applied to find the most appropriate manufacturing conditions. The most promising resin M-27 was found to be fitting the requirements for the produced objects (Fig. 4).
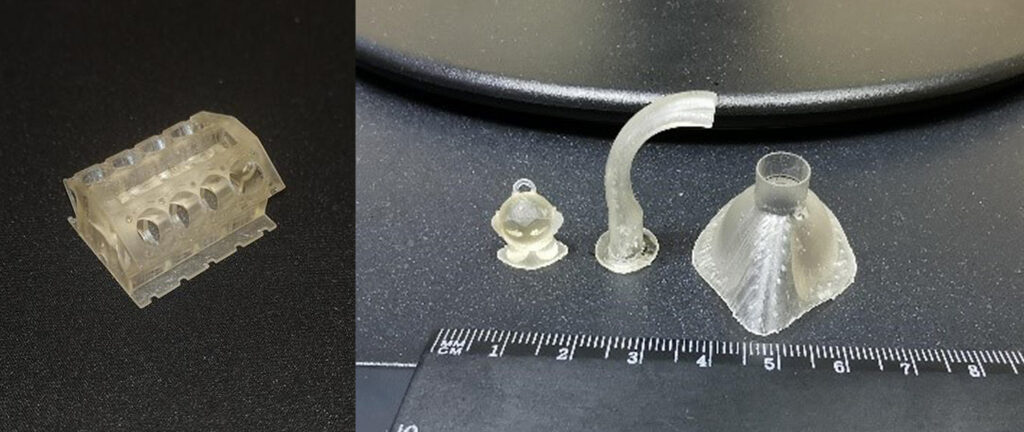
Once it was realized, the manufacturing was transferred to 3D Creative. Despite the differences of the equipment switching from Digital Light Processing (DLP) to Liquid Crystal Display (LCD) techniques and from 385 nm to 405 nm irradiation wavelengths, judging from geometrical and mechanical properties the produced objects revealed suitability for the intended use.
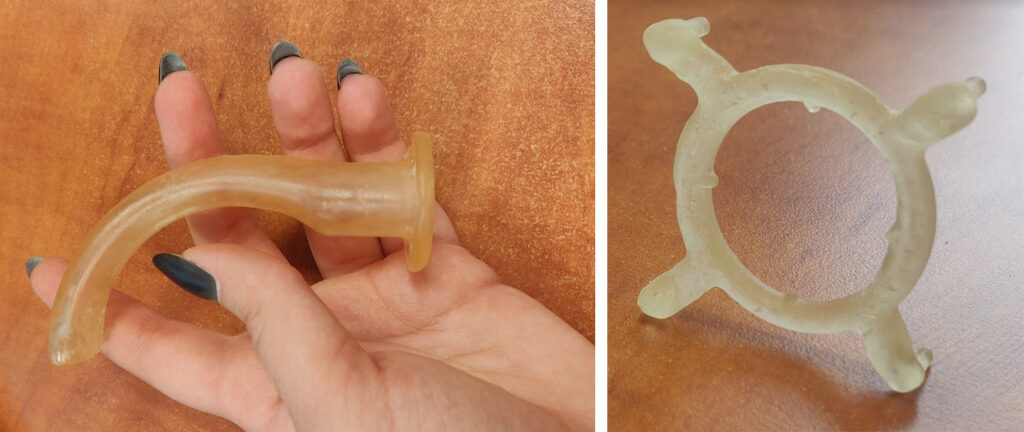
Plant-based bioresins replace petroleum-based resins for AM
In conclusion, the performed interdisciplinary experimental work shows practical validation of the approach proposed as demonstrator via the ECOLABNET project scheme. It proves that plant-based bioresins are suitable candidates for replacing petroleum-based synthetic resins for rapid prototyping and additive manufacturing.
The solution is highly eco-innovative, empowering saving of time, transportation, raw materials resources. This new generation material also contributes to the reduction of climate pollution as it is naturally degradable and can be recycled afterwards. Additionally, it is driven by the flexibility of 3D printing it initiates and supports creativity enhanced new solutions to old problems.
Acknowledgment: The research was funded by the EU ERDF, through the INTERREG BSR Programme, (ECOLABNET project #R077).
Reference
- E. Skliutas, M. Lebedevaite, S. Kasetaite, S. Rekštytė, S. Lileikis, J. Ostrauskaite, M. Malinauskas, A Bio-Based Resin for a Multi-Scale Optical 3D Printing. Sci. Rep 10, 9758 (2020). https://doi.org/10.1038/s41598-020-66618-1