Writers: Simo Huhtanen, Rathish Rajan, Egidija Rainosalo (Centria UAS) | Centria University of Applied Sciences, Kokkola, Finland | egidija.rainosalo@centria.fi
The plugs and moulds are a very crucial part of the entire production chain of fibre-reinforced polymer composites (FRP), which are used in such industries as building and construction, wind blades, boat building, automotive, aircrafts and sporting goods. Thus, the quality, cost and lead time of the mould manufacturing will influence the overall cost of the FRP production.
Traditionally plug is made by milling with CNC shape of product from tooling board, which can be e.g. polyurethane, EPS, epoxy, wood, MDF or alike boards or blocks. Milled plug surface is perfected by applying several layers of plaster resins, FRP and surface coats. Every layer is machined by CNC and /or by hand (Fig 1). The dust created from the milling and sanding of this plug/mould building materials is harmful to workers, create safety concerns in the production facility and compromises the production quality. In general, in spite of using CNC for several operations, mould making is labour intensive manufacturing process and lead time of such a process might be up to several weeks. Moreover, the recycling of such product is a challenge due to the combination of multiple materials.
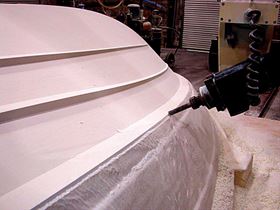
Additive manufacturing (AM) or 3D printing is an emergent technology for manufacturing customised products and has potential for production of high-quality plugs and moulds. The most common at the moment is fused filament fabrication (FFF or FDM) method, which utilises thermoplastic filaments for manufacturing parts. However, it has certain limitations when producing large-sized parts due to the smaller working size in the currently available FDM based printers, production of filament is an additional process step which adds costs of raw materials. For manufacturing large-sized parts, raw materials in the form of granules are preferable instead of filaments due to the cost reduction and also due to the availability of a significantly wider range of materials.
In Ecolabnet-project, Centria is evaluating various thermoplastic materials to 3D-print moulds suitable for manufacturing FRP-based products and optimising fused granule fabrication (FGF) technology to print large parts. Most common resins used in FRP production are epoxy and polyester resin based. Mould material have to be resistant to styrene, peroxides, diamines hardeners used in those resins. Mould material needs to be resistant to resin chemicals, have sufficient HDT to withstand the heat of resin curing reaction during FRP product manufacturing. Additionally, it has to be 3D printable, low thermal shrinkage/expansion to reduce warping and also affordable as moulds can be large.
The most traditional 3D-printing materials, PLA and ABS, cannot withstand the chemical of resins, new materials need to be found. 3D printing of large parts from commercially available materials has also challenges related to residual stresses which cause warping, reduced mechanical properties due to voids and not optimal adhesion between layers. We have chosen polypropylene as it is chemically resistant and affordable. We compounded it with 40% of wood flour, which reduces warping, increases strength and stiffness in elevated temperatures and improves machinability and sanding properties. Moreover, wood flour is replacing 40% of fossil-fuel-based polymers, the material is recyclable and can be reused for the production of new products. Use of such material in fused granule fabrication (FGF) is expected to reduce overall life cycle costs of mould.
Set-up of the FGF printing at Centria is presented in Fig 2. pellet extruder is attached to the robot arm and could print parts up to 678 dm3 in size. Printing head can also be attached to CNC machine readily available at most mould making companies. This way investment cost for setting 3D printing can be reduced, also CNC machine can be utilized more effectively.
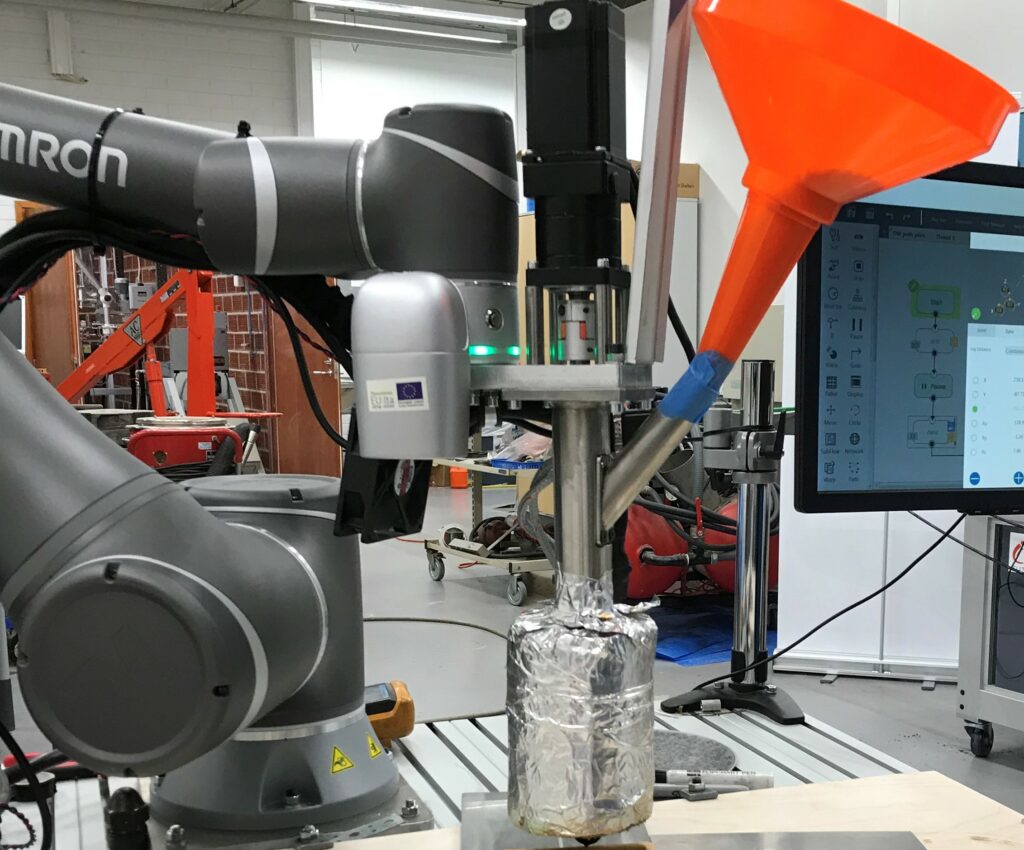
Steps to produce 3D printed mould are visualised in Figure 3. After printing, raw mould has a very rough surface and it should be smoothened to the desired degree. Milling of raw print can be performed by CNC and next steps are similar to current practises in the composites industry. The surface is painted with conventional composite toolcoat. Toolcoat is then cured, sanded and polished in the same way as the composite industry currently finishes moulds.
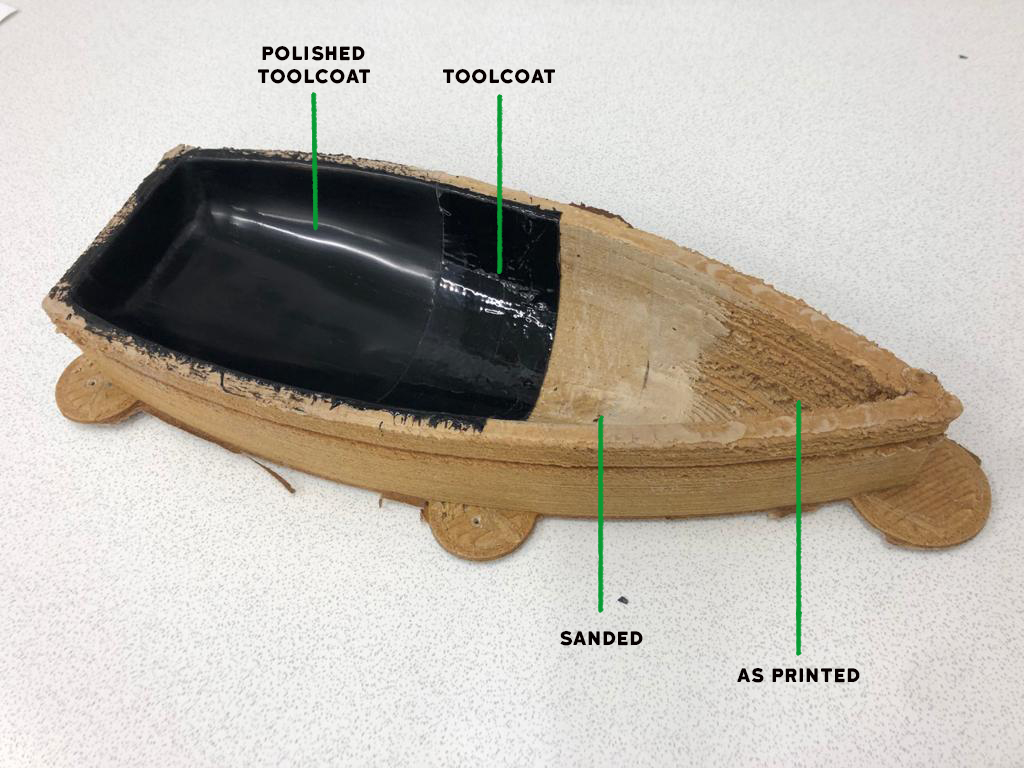
We manufactured test mould (Figure 4) and used it for manufacturing gelcoated composite part. According to visual evaluation, we obtained high-quality surface part. Thus, 3D printing of composite tooling using fused granular fabrication (FGF) seems to be a viable method.
Using 3D printing technology whole mould can be made from the same material and only a thin layer of toolcoat is needed to reach high gloss surface of the tool. This opens the possibility for recycling of manufactured moulds and use of recyclate as a raw material for manufacturing new moulds. Thus, our next development will be testing the use of recycled mould for 3D printing new tools.
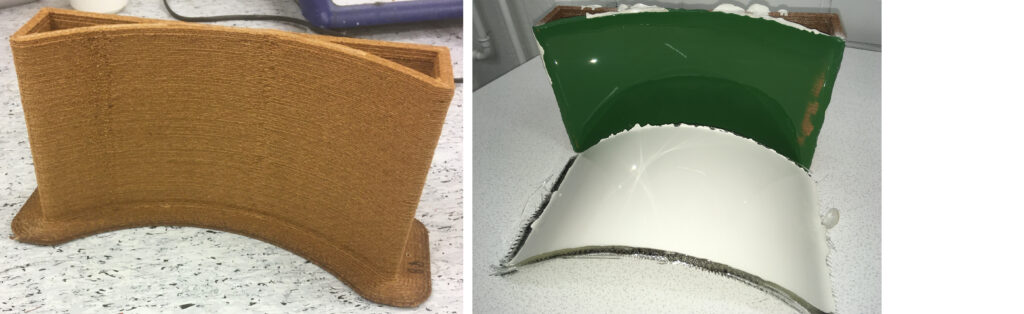
Acknowledgments: The research was funded by the EU ERDF, through the INTERREG BSR Programme, (ECOLABNET project #R077).
References
[1] R. Stewart Mould and tooling advances promising for composites, https://www.materialstoday.com/composite-applications/features/mould-and-tooling-advances-promising-for/.