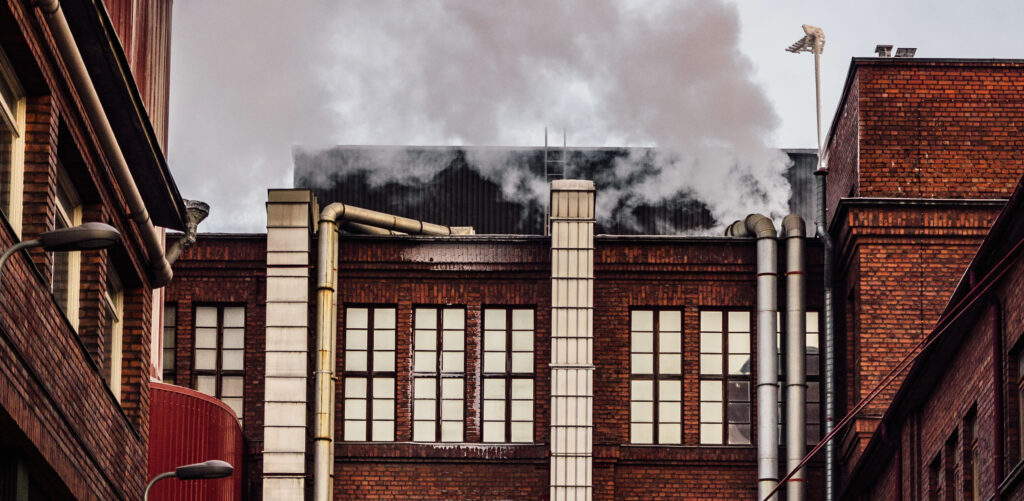
Writer: Janne Pekkala | Concept designer | Muova
Nowadays, many manufacturing companies are developing services in order to offer integrated sets of product and services that better satisfy customer needs. Such products-service systems (PSS) have significant ecological potential as the finished products are better utilized through complementary services.
The focus is on the process and function
At the heart of product-service systems is the idea of providing the function that the customer needs rather than providing the ownership of the product. For example, customers typically lease the copy machine rather than invest capital on it. Companies like Xerox and Canon lease a copy machine and take care of ink cartridge delivery, troubleshooting, maintenance and repair through their service network. Customers pay for the copies only and do not have to worry about spare parts or other additional costs.
Better customer experience through digital services?
As mentioned earlier, product-service systems can lower the threshold for acquiring a product (e.g. leasing services, financial services). Furthermore, usage data can be collected through sensors and analysed to useful information for further utilization. Information about the usage enable customers to feel being better in control as they can make informed decisions based on reliable facts. In addition, digital technology enables intelligent maintenance services and remote equipment management.
Getting closer to the customer
Manufacturing companies can get closer to their customers whilst providing services. The company not only delivers the product but may take care of various stages in the product life cycle, from manufacturing to disposal and recycling. Providing lifecycle services enables close communication with the customer and the company receives customer feedback about the usage and build better understanding of the customer’s needs.
Resource-wise innovations
When the focus of the manufacturing company shifts from product delivery to lifecycle services, it becomes worthwhile to consider the optimal use of resources. Replacement of parts, disassembly, reuse and recycling need to be considered and planned already in the product design and development stage.
Designing product-service systems
At Muova, we have been involved in developing several PSS for both large and small manufacturing companies. We have noticed that it is important to study carefully both the business models, processes and expectations of the end customers. Co-development methods enable customers to be involved in development work and achieve a common understanding of development goals.
We have developed our capability to combine product design and service design methods flexibly and, on a case-by-case basis. Design thinking provides effective tools to map and identify customer experiences, gains, pains, and expectations. The main benefits of design seem to be the ability of concretizing the customer’s business processes into a visual form and to propose solution concepts that are tightly based on customer research.
How to digitalize the PSS development?
We believe that the digitalization of the service development will increase in the future. We all know that 3D software revolutionized the product development. Respectively, it is important to ask how digitalization can improve service development and design process. In Muova, we have developed a prototyping laboratory for industrial services, which allows the service processes to be modelled and studied in a virtual world. This enables the documentation of service processes and, above all, the testing of new services before building a service system. More information about our CoprotoLab can be found at https://coprotolab.fi/
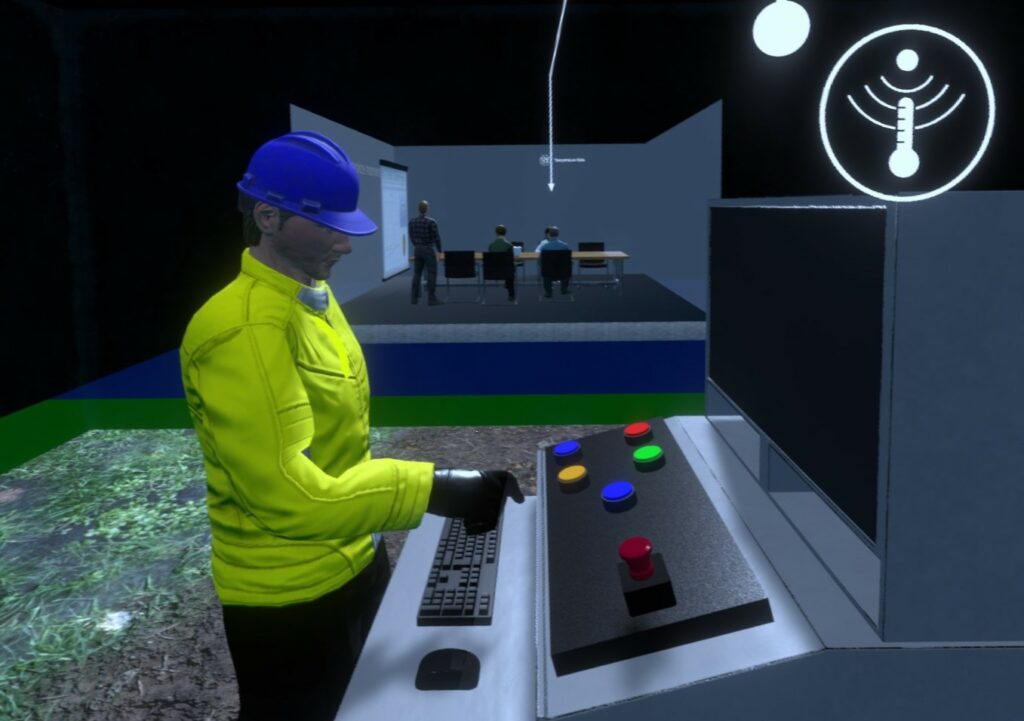